Emergency Lighting and Sensing
Industrial Designer/Mechanical Design Engineer for the products below. Click each product to be forwarded to it’s specification page.

Description
Macolighting
December 2012 - November 2014
Product development of emergency lighting equipment designed in Australia and manufactured in China. Products were holistically designed taking into consideration the whole design process. Stages of the design process include; customer requirements, initial sketches, DFMEA, 3D modelling, material selection, stress analysis using FEA, manufacturing drawing creation, prototyping with 3D printers and mold iterations until an acceptable product had been achieved to be released for production. Each design was optimised in terms of cost, aesthetic design and material wastage.
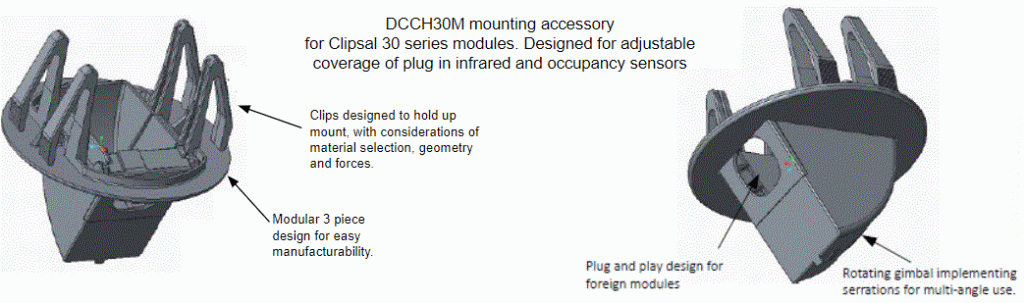
The DCCH30M mounting accessory requirements called for a device that could rotate 360 degrees in all directions while still being able to be manufactured easily and be relatively inexpensive. The accessory needed to be able to accommodate a pre-manufactured plug & play product. This design was iterated over and over to make sure that it was optimised for the least amount plastic used while still maintaining strength. It was designed as a modular 3 piece product so that it could be easily manufactured and assembled.
Analytical tools and Optimisation
All products were optimised through finite element analysis (FEA) and moldflow simulation software to make sure that the geometry and material of the products could withstand external environmental stresses.
The Ledfire 3 required a design that accommodated for a heat-sink that was already used in other products. In order to reach emergency lighting standards, experimentation with light exposure dependant on the angles produced by the plastic and LEDs was undertaken. Stress analysis techniques were done repeatedly to make sure that spring loads did not cause failure in plastic due to installation (FEA).
The above illustration shows flow marks of the Ledfire 3 plastic that are visual distortions on the surface of the product due to high wall thickness on the other side. The product is optimised to reduce the visibility of these distortions.
Liaising with manufacturers and suppliers
After analysis of the model, manufacturer drawings were created to relay which dimensions are of priority in order to keep within the product requirements. This document may have a few iterations in order to make it easy for the manufacturer to produce, as well as keeping to the correct tolerances that the engineer has prescribed. Once the product was approved it then went through standard approvals and is released for production.
As part of my work at MacoLighting I worked in Dongguan, China for 2 months overseeing the transition of these products to be released for production.
The Ledfire surface mount requirements called for creating the same LED lighting in a surface mount enclosure for applications where cavities can not be made in the ceiling. The challenge of this product was the accommodation of ever changing internal hardware. The design had many iterations especially for the lid clipping mechanism.
The above illustration shows the manufacturer drawing of the Ledfire III Surface Mount. Due to the intellectual property agreement, details have been omitted.
Prototyping for simulating production versions
Once the manufacturer drawings are completed, prototypes are made to make sure that fits and limits of mating parts are acceptable. Prototypes are made as an easy way to confirm the design without the expensive process of cutting metal to create a mold. Once this is approved the design can be utilised with more confidence when creating the mold for mass manufacture.
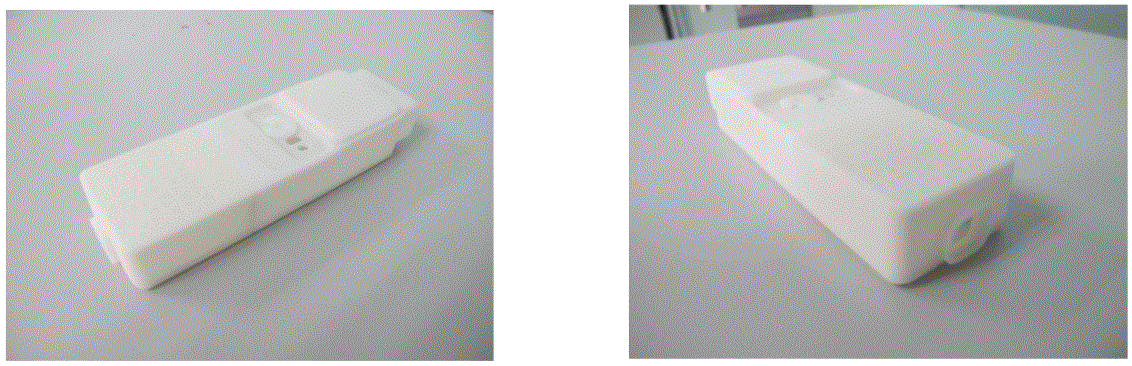